Наши поставщики
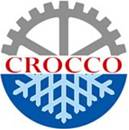
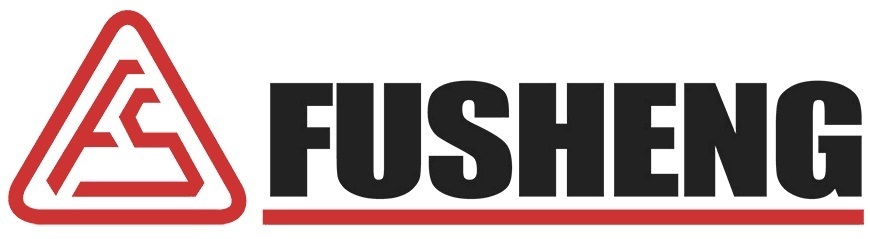
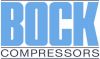

АВТОР: ВИКТОР ВЕЛЮХАНОВ (ГЕНЕРАЛЬНЫЙ ДИРЕКТОР ООО «ФРИГОТРЕЙД»)
«Московская Пивоваренная Компания» является современным быстро развивающимся предприятием, появившимся на российском рынке в 2008 г с годовой производственной мощностью 2,4 млн. гектолитров, а в настоящее время развившим ее до 8,0 млн. гектолитров в год. Среди ценностей, провозглашаемых предприятием, готовность к переменам и инновациям и экономичность. Предлагая лучшую цену на свою продукцию, предприятие должно производить ее с меньшими затратами, при этом экономия не должна сказываться на качестве выпускаемой продукции.
В начале 2011 г ООО «Фриготрейд» получило этот проект, пройдя через конкурс, который был организован «Московской Пивоваренной Компанией» для реализации этого проекта, и выполнило работы по проектированию, поставке и монтажу дополнительного оборудования с целью повышения энергоэффективности, снижения расходов на эксплуатацию и снижения рисков простоя предприятия.
Аммиачная система холодоснабжения предприятия предназначена для подачи хладагента (аммиака) и хладоносителя (пропиленгликоля) в технологические цеха с целью охлаждения проточных технологических аппаратов, танков брожения и хранения пива, пастеризаторов. Также система холодоснабжения обеспечивает подачу хладагента в теплообменные аппараты охлаждения пивоваренной и дегазированной воды, в воздухоохладители для технологического кондиционирования помещений бродильно-лагерного отделения, помещения склада хмеля, дрожжевого отделения и ряда других помещений.
На данном предприятии используется система холодоснабжения с насосной подачей жидкого аммиака в испарители и промежуточным хладоносителем с закрытым баком-аккумулятором. Эта система обеспечивает холодом все технологическое производство и включает в себя компрессорное, теплообменное, емкостное и насосное оборудование. Холодильная установка работает на две температуры кипения хладагента: -6°С и 0°С.
При производстве пива выделяется углекислый газ, который собирается, очищается, сжижается и хранится в соответствующих танках. При потребности пивоваренного производства в газовой углекислоте жидкая фаза поступает из танков хранения и газифицируется, после чего перегретый газ подается на производство и используется для вытеснения пива из емкостей, продувки трубопроводов и в других технологических целях. В летнее время газификация углекислоты происходит в существующих на предприятии воздушных газификаторах. Однако зимой из-за низкой температуры окружающего воздуха производительности этих воздушных газификаторов недостаточно для обеспечения постоянно растущих потребностей производства данного предприятия.
Техническое перевооружение аммиачной системы холодоснабжения в рамках заключенного договора включало в себя следующие работы:
Резервный теплообменник-испаритель после завершения монтажных работ
Пластинчатый теплообменник-газификатор углекислоты с центробежным насосом подачи хладоносителя
Температура хладоносителя (пропиленгликоля) на входе в газификатор 0°С, на выходе из него -4°С. Температура жидкой углекислоты на входе в газификатор -25°С, температура газообразного СО2 на выходе из газификатора -15°С. Для подачи хладоносителя в газификатор наши специалисты установили центробежный насос производительностью 115 м3/ч с преобразователем частоты. Хладоноситель, поступающий на вход газификатора, отбирается с линии возврата хладоносителя с производства и имеет температуру 0°С. Углекислота испаряется в газификаторе, принимая тепло от промежуточного хладоносителя (пропиленгликоля). Испарившаяся углекислота после выхода из испарителя-газификатора поступает в существующий в системе воздушный теплообменник для перегрева газа и далее поступает на производство.Система управления узлом газификации углекислоты и регулирующая арматура позволяют автоматически регулировать температуру углекислоты на выходе от -15°С и выше. Управление осуществляется по температуре воздуха на входе в воздушный газификатор и по температуре газообразной углекислоты на выходе. При температуре воздуха на входе ниже +25°С вся углекислота выпаривается в гликолевом теплообменнике-газификаторе. При температуре воздуха на входе воздушного газификатора выше +25°С часть жидкой углекислоты поступает в него, минуя гликолевый теплообменник-газификатор, при этом температура углекислого газа на выходе воздушного газификатора не должна опускаться ниже +5°С.
При этом сам процесс испарения жидкой углекислоты позволяет дополнительно охлаждать хладоноситель (пропиленгликоль), использующийся в технологическом процессе, что позволяет экономить электроэнергию, затрачиваемую на его охлаждение с помощью холодильных машин. Подача углекислоты в испаритель-газификатор осуществляется под действием перепада давления; давление в танках хранения жидкой углекислоты составляет 1,58 Мпа (изб).
Спроектированный и установленный ООО «Фриготрейд» теплообменник-газификатор с насосом, имеющим частотный привод, и исполнительными механизмами является отдельной установкой, интегрированной в действующую систему холодоснабжения предприятия. Система управления этой установкой реализована нашими специалистами на базе контроллера фирмы Siemens SIMATIC c сенсорной панелью. В качестве регулирующих исполнительных механизмов используются преобразователь частоты Danfoss, моторный клапан Danfoss ICAD, электромагнитные клапаны. Система управления выполнена с учетом дальнейшей модернизации, увеличения функциональности и интеграции в глобальную систему управления «Умный завод».
Панель оператора со схемой и основными параметрами технологического процесса
Монтаж и прокладка трубопроводов осуществлялась в рамках установленного ООО «Фриготрейд» оборудования. Толщина стенок трубопроводов при проектировании выбиралась по расчетному рабочему давлению среды внутри трубы и с учетом технологических и коррозионных коэффициентов, исходя из расчетного срока службы трубопроводов не менее 20 лет. Прокладка горизонтальных участков трубопроводов проводилась с уклоном в полном соответствии с «Рекомендациями по устройству и безопасной эксплуатации технологических трубопроводов» и ФНиП «Правила безопасности химически опасных производственных объектов». Контроль сварных соединений трубопроводов проводился ультразвуком.После монтажа осуществлялась продувка трубопроводов для удаления окалины и механических загрязнений. Все трубопроводы, имеющие температуру стенки трубы ниже +12°С, были теплоизолированы. При проведении теплоизоляционных работ поверхность трубопроводов очищалась, после чего на нее наносилось антикоррозионное покрытие. В качестве теплоизоляционного материала для изоляции труб установленного оборудования и арматуры использовался вспененный синтетический каучук с закрыто-пористой структурой, который в настоящее время является эффективным теплоизоляционным материалом с высокими теплофизическими и эксплуатационными характеристиками. Теплоизоляция крепилась к трубам клеем, при этом поперечные и продольные швы между приклеенными листами изоляции были заклеены самоклеющейся лентой.
После монтажа и теплоизоляции вновь установленных участков трубопроводов с хладагентом на них были нанесены опознавательные кольца согласно рекомендациям ФНиП «Правила безопасности химически опасных производственных объектов».
Размещение вновь установленного холодильного оборудования и трубопроводов выполнено, исходя из требований обеспечения свободного доступа к оборудованию и трубопроводной арматуре для их удобного обслуживания и ремонта. Проходы между существующими строительными конструкциями и вновь установленным оборудованием согласно указанным выше рекомендациям ФНиП должны быть не менее 1 м, а между отдельно стоящими колоннами и оборудованием — не менее 0,7 м.
Специалистами фирмы ООО «Фриготрейд» установлено 46 новых самодействующих предохранительных клапанов для защиты содержащего аммиак холодильного оборудования от разрушения в случае пожара. Отвод паров хладагента при срабатывании предохранительных клапанов производится по аварийным трубопроводам, рассчитанным на сброс паров от подключенного к нему аппарата системы холодоснабжения.
Установленные предохранительные клапаны с трубопроводами аварийного сброса хладагента
Заказчику была передана рабочая документация по данному проекту на электронном и бумажном носителях.